10.3. КЕРАМИЧЕСКИЕ МАТЕРИАЛЫ
10.3. КЕРАМИЧЕСКИЕ МАТЕРИАЛЫ
В настоящее время под керамическими материалами подразумеваются не только такие мате-
риалы, как фаянс, фарфор, огнеупоры, строительная керамика, абразивы, эмали, цементы и стекла, но также неметаллические магнитные материалы, сегнетоэлектрики, синтетические монокристаллы и другие виды, еще не существовавшие несколько лет назад.
Слово керамика происходит от греческого слова «keramos», что означает горшечная глина или фаянс. Традиционная керамика изготавливается силикатной промышленностью, которая занимается главным образом производством изделий из глин, цемента и силикатных стекол.
Изготовление фаянса путем формования и обжига глиняных изделий известно давно. В раскопках находят изделия из обожженной глины, имеющие возраст около 17 тыс. лет. В Египте около 5 тыс. лет до нашей эры существовало промышленное производство керамических изделий.
Производство силикатных стекол известно также с древних времен. Эмали на каменных украшениях и изделия из стекла были известны 12–5 тыс. лет до нашей эры, а в Египте около 2 тыс. лет до нашей эры имелась достаточно развитая стекольная промышленность.
Производство цементных материалов получило развитие не более 200 лет назад.
В России гончарное производство было широко распространено уже в X–XIII вв. Глиняные изделия, найденные при раскопках Великого Новгорода, указывают на высокое мастерство русских гончаров.
В XVIII в. в России был создан фарфор и стало осваиваться его промышленное производство. В 1756 г. под Москвой строится фарфоровый завод. В 1798 г. начинает выпускать продукцию первый фаянсовый завод вблизи Киева.
В XIX в. керамическая промышленность России добивается значительных успехов. Центрами силикатной промышленности становятся такие города, как Москва, Санкт-Петербург, Харьков и др.
Если провести анализ керамической промышленности развитых стран, то можно увидеть, что наибольший объем занимает производство натрий- и кальцийсиликатных стекол. Затем наиболее крупным по объему является производство извести и цемента (здесь большая доля падает на производство строительного цемента). Наиболее разнообразная группа изделий относится к тонкой керамике, которая включает фаянс, фарфор и другие виды материалов с тонким черепком. К следующей распространенной группе традиционной керамики относятся эмали, выпускаемые для покрытия металлов, затем следуют строительные материалы, огнеупоры и абразивные материалы.
Несмотря на то что силикатная (традиционная) керамика составляет наибольший объем выпускаемых керамических изделий и материалов, в последнее время разрабатываются разнообразные типы новых керамических материалов, которые обладают уникальными свойствами. Такие материалы разработаны либо для применения при очень высоких температурах и при этом обладают большой механической прочностью, высокими значениями электрического сопротивления и химической стойкостью, либо при исследовании материалов, когда открываются новые свойства, которые позволяют создавать принципиально новые устройства или существенно улучшить параметры существующих (например, открытие варисторного и позисторного эффектов, высокотемпературной сверхпроводимости и гигантского магнитного сопротивления в оксидных перовскитовых структурах).
В последние 50 лет было создано много новых керамических материалов [10.8–10.13]:
керамика чистых оксидов для специальных электротехнических или огнеупорных изделий характеризуется высокими значениями ряда свойств и стабильностью; ее изготовляют чаще всего на основе корунда Аl2O3, диоксида циркония ZrO2, оксида магния (MgO), шпинели MgAl2O4 и форстерита Mg2SiO4;
ядерное топливо на основе использования диоксида урана UO2, который сохраняет свои свойства при длительном использовании в ядерных реакторах;
магнитная керамика, уникальные электрические свойства которой позволяют использовать ее в высокочастотной радиоэлектронике;
монокристаллы разнообразных материалов, которые используются в настоящее время в различных областях техники. В качестве примера можно привести монокристаллы сапфира, выращиваемые из расплава, и крупные кристаллы кварца, выращиваемые в гидротермальных условиях;
металлокерамика, играющая большую роль в машиностроении; представителями этой группы материалов являются различные карбиды на металлической связке, а также смеси хромосодержащих сплавов с оксидом алюминия;
сегнетоэлектрическая керамика на основе титана бария, открытого в 1944 г. Б.М. Вулом (СССР), которая имеет высокую диэлектрическую постоянную и может служить активной и пассивной средой во многих электротехнических приборах и устройствах;
бессиликатные стекла, которые имеют особое применение благодаря прозрачности в инфракрасной части спектра;
ситаллы, технология которых является достаточно новой и заключается в формовании изделий из стекла с последующей термообработкой, обеспечивающей протекание процессов образования центров кристаллизации и контролируемого роста кристаллов с получением однородного тонкозернистого стеклокристалличес-кого материала.
Кроме того, в настоящее время производят и используют большое количество других новых керамических материалов, не известных 10 или 20 лет назад. С этой точки зрения керамическая промышленность является одной из наиболее быстро развивающихся отраслей индустрии, продукция которой постоянно совершенствуется. Необходимость в новых керамических материалах обусловливается постоянными потребностями в создании более совершенных и новых изделий.
Быстрое развитие электротехнической и радиотехнической промышленности требует роста производства, электротехнической керамики и высококачественных изоляторов.
Основными материалами для изготовления изоляторов являются керамические материалы, среди которых ведущее место занимает фарфор [10.13–10.19]. В России этот замечательный материал был создан Д.И. Виноградовым, современником М.В. Ломоносова. В результате многочисленных исследований. Д.И. Виноградов получил первые образцы отечественного фарфора (порцелина) [10.20] и основал первый фарфоровый завод в России «Порцелиновая мануфактура» в 1744 г. До нас дошли 23 рецепта фарфоровых масс и 10 рецептов глазурей, разработанных Д.И. Виноградовым, которого по праву можно считать основоположником производства русского фарфора [10.14, 10.20, 10.24].
В России до 1917 г. изоляторная промышленность как самостоятельная отрасль не существовала. Электротехнические изделия из фарфора — телефонные и телеграфные изоляторы, ролики, розетки и другие изделия — изготовлялись на заводах, основной продукцией которых являлась фарфоровая посуда. Это заводы в Санкт-Петербурге, Я. Эссена в Риге, Славянске, Бердникова в Житомирской области и др. Исключение составлял завод С.П. Чоколова (ныне завод «Изолятор»), основанный в 1894 г. под Москвой и специализировавшийся на выпуске электротехнических изделий из фарфора. Эти заводы выпускали преимущественно электротехнический фарфор для установок низкого напряжения.
В конце XIX в. эти заводы начали выпуск телефонных и телеграфных изоляторов, электроустановочных изделий (роликов, розеток и др.) [10.14, 10.15]. После Октябрьской революции ряд заводов полностью переходит на изготовление электротехнической продукции: завод Корниловых в Петербурге, ныне завод «Пролетарий», завод им. Артема в г. Славянске, завод «1 Мая» в Токаревке Житомирской области. Производство электротехнических фарфоровых изделий, несмотря на отсутствие на заводах механизации, достигло значительного совершенства, и высокое мастерство рабочих керамистов заслуженно и неоднократно отмечалось на всемирных выставках.
Объем отечественного производства электротехнического фарфора не мог удовлетворить спроса развивающейся электротехнической отрасли. Значительная часть потребности в изоляторах низкого напряжения и почти полностью высокого напряжения удовлетворялась ввозом из-за границы.
Одна из первых попыток выпуска отечественных изоляторов высокого напряжения относится к 1906–1907 гг., когда заводом С.П. Чоколова была изготовлена партия штыревых изоляторов на напряжение 6–10 кВ довольно сложной конструкции, имевших три выступающие «юбки». Эти изоляторы были направлены для испытания в Германию в лабораторию завода ГЕШО (Гемсдорф-Шомбург). Все изоляторы выдержали испытания и были рекомендованы к производству. Однако завод С.П. Чоколова не организовал массового выпуска штыревых изоляторов этого типа, что можно объяснить сложностью их конструкции и трудностью конкуренции с иностранными фирмами.
Значительных успехов в выпуске высоковольтных изоляторов добился завод Я. Эссена в Риге. В 1912–1915 гг. этим заводом выпускались изоляторы на напряжение до 20 кВ преимущественно по чертежам германских фирм. В 1915 г. завод Я. Эссена был эвакуирован в г. Славянск, где Я. Эссен купил у фабриканта М.С. Кузнецова посудную фабрику, в корпусах которой было размещено оборудование, вывезенное из Риги.
В годы первой мировой войны Россия была отрезана от заграничных поставщиков. Для удовлетворения острой потребности в изоляторах высокого напряжения славянский завод, а также некоторые другие предприняли попытки наладить массовый выпуск изоляторов высокого
напряжения. Эти попытки не увенчались успехом, ввиду того что заводы не смогли овладеть особенностями обработки электрокерамики и режима сушки и обжига. Кроме того, заводы того времени не располагали испытательным оборудованием высокого напряжения и были лишены возможности корректировать конструкцию и технологию производства изоляторов.
Первые партии изоляторов на напряжение 35 кВ были выпущены по заграничным образцам в 1919–1920 гг. заводом им. М.В. Ломоносова в Петрограде ив 1921 г. Дулевосим заводом фарфоровой посуды. Изготовленные по технологии, обычной для производства хозяйственного фарфора, эти изоляторы после установки их на линиях электропередачи через короткий срок выбыли из эксплуатации вследствие массовых пробоев.
Опыт показал, что производство изоляторов высокого напряжения требует специальной технологии. Для этой цели электропромышленности были переданы четыре завода, которые ранее частично выпускали изоляторы и фарфоровые изделия («Изолятор», «Пролетарий», им. Артема и «1 Мая»).
Центральным электротехническим советом (ЦЭС) были утверждены разработанные в 1919 г. Петроградским политехническим институтом под руководством М.А. Шателена первые технические условия на высоковольтные фарфоровые изоляторы.
Большую роль в развитии отечественной керамической промышленности сыграла организация в 1919 г. в Петрограде Государственного научно-исследовательского керамического института.
В 1921 г. по заданию Главэнерго А.А. Горевым были разработаны отечественные конструкции штыревых изоляторов на напряжение 6–35 кВ. Эти изоляторы выпускались заводами «Изолятор» и «Пролетарий» до 1924–1926 гг. [10.18–10.19].
В период 1926–1935 гг. широким фронтом велись работы по реконструкции изоляторных заводов и оснащению их новым оборудованием. В 1934 г. завод «Пролетарий» ввел в эксплуатацию первую туннельную печь непрерывного действия длиной 121 м для обжига электроустановочных изделий. На заводе им. Артема в 1940 г. введены в эксплуатацию печи периодического действия с шестью камерами общей вместимостью 450 м3 и туннельная печь, разработанная в СССР.
Сооружение Свирской ГЭС и линии электропередачи на напряжение 220 кВ потребовало подвесных изоляторов с гарантийной механической прочностью 6,86?104 Н. Производство таких изоляторов было освоено в 1932 г. на заводе им. Артема и в 1935 г. на заводе «Пролетарий».
В начале 1923 г. на заводе «Изолятор» была сооружена изоляторная лаборатория с испытательной установкой на напряжение до 300 кВ и специальной машиной для механических испытаний изоляторов, что позволило планомерно проводить работы по изучению характеристик зарубежных и разрабатываемых отечественных изоляторов. В том же 1923 г. на заводе «Изолятор» была разработана и выпущена первая партия штыревых изоляторов на напряжение 35 кВ технологически приемлемой формы типа ШИ. Опыт эксплуатации этих изоляторов дал удовлетворительные результаты, и они были включены в первый общесоюзный стандарт (ОСТ 3370) и выпускались до 1939 г. [10.21].
В период 1923–1925 гг. осваивается серийное производство линейных изоляторов высокого напряжения на заводах им. Артема и «Изолятор» и аппаратных изоляторов на заводе «Пролетарий». Производство аппаратных изоляторов представляло наибольшие трудности вследствие сложности их профилей и примитивности оборудования, которым в то время были оснащены наши заводы. Значительную помощь заводам в области испытаний и корректирования первых конструкций изоляторов оказали коллективы научных работников ИНХ им. В.Г. Плеханова (Б.И. Угримов), а также ЛЭТИ (А.А. Смуров и его сотрудники). В 1925 г. для создания новых изоляторов было организовано Техническое бюро изоляторных заводов Электротехнического треста Центрального района (ЭТЦР), руководителем которого являлся Н.В. Головкин. Экспериментальной базой бюро был завод «Изолятор», на территории которого оно помещалось. Бюро разработало конструкции первых отечественных подвесных изоляторов (типа ПГ-22), проводило работы по исследованию, созданию и модернизации ряда конструкций изоляторов и арматуры для них. В бюро выросла группа инженеров-специалистов в области керамической изоляции (А.В. Ефимов, Л.И. Федоров и др.).
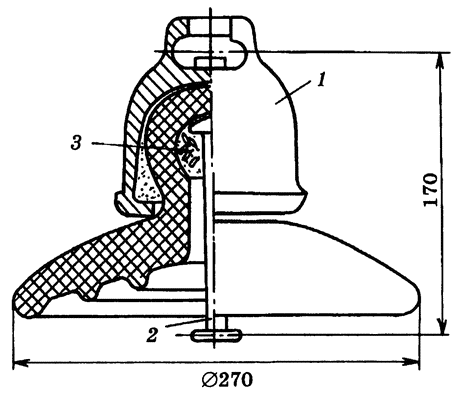
Рис. 10.2. Подвесной фарфоровый изолятор ПГ-22 (первая отечественная конструкция подвесного изолятора)
Важным этапом в развитии отечественного изоляторостроения явились разработка и технологическое освоение производства подвесных изоляторов для строившихся линий электропередачи напряжением 110 кВ. В результате проведенных исследований подвесных изоляторов, поставлявшихся СССР заграничными фирмами, была разработана отечественная конструкция подвесного изолятора ПГ-22 (рис. 10.2). В этом изоляторе шапка 7 закреплялась на головке изолятора при помощи цементной замазки, заделка же стального стержня 2 производилась при помощи стальных шпилек 3, заливаемых легкоплавким сплавом, состоящим из свинца и сурьмы. Серийный выпуск подвесных изоляторов был начат в 1927 г., что позволило уже в годы первой пятилетки отказаться от импорта изоляторов этого класса. Впоследствии (1938–1939 гг.) на освоении работ, проведенных изоляторной лабораторией ВЭИ, в конструкцию подвесного изолятора были внесены изменения (изолятор П-4,5): заделка шапки и стержня производилась на цементной замазке с применением эластичных битумных покрытий. Этот тип изолятора вошел в первый общесоюзный стандарт на фарфоровые изоляторы (ОСТ 3370) в 1930 г., а также в ГОСТ 6490–53. Для повышения качества продукции и производительности заводов большое значение имели работы, проведенные в 1926–1928 гг., по переводу печей (горнов) с твердого топлива (дров) на жидкое и усовершенствованию процессов обжига электротехнического фарфора.
Дальнейшее развитие электроизоляторного производства связано с развитием трансформаторе- и электроаппаратостроения, а также сооружением линий электропередачи на напряжение 220 кВ.
В 1931 г. завод «Изолятор» начал производство маслонаполненных фарфоровых вводов на напряжение 110 кВ, которые изготовлялись по чертежам американской фирмы ДЖИИ, а затем по усовершенствованным заводским конструкциям.
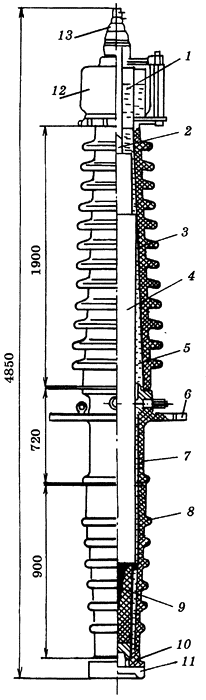
Рис. 10.3. Фарфоровый маслонаполнениый ввод с внутренней бумажно-масляной изоляцией конденсаторного типа
1 — гайки; 2 — токоведущая труба; 3 — верхняя фарфоровая покрышка; 4 — обмотка из кабельной бумаги; 5 — трансформаторное масло; 6 — опорная поверхность втулки; 7 — соединительная втулка; 8 — нижняя фарфоровая покрышка; 9 — цилиндрические обкладки; 10 — стакан; 77 — экран; 12 — масляный расширитель; 13 — контактный зажим
В 1932 г. для линий электропередачи на напряжение 220 кВ были разработаны и освоены в производстве подвесные изоляторы типа П-7 с гарантийной механической прочностью 6,86?104 Н. Освоение в производстве вводов на напряжение 220 кВ потребовало большего времени, чем для вводов на напряжение 110 кВ, так как их конструкция была более сложной. Потребовалась разработка специальной технологии
сушки, обжига и охлаждения этих крупногабаритных керамических конструкций. Внутренняя изоляция ввода, которая изготовлялась по американским чертежам, не обеспечивала необходимой надежности. Группой специалистов заводов «Изолятор», «Электроаппарат», Московского электрозавода и ВЭИ изоляция ввода была улучшена, после чего начался серийный выпуск вводов на напряжение 220 кВ (рис. 10.3).
В 1932–1933 гг. были разработаны конструкции установок для непрерывного испытания изоляторов высоким напряжением, что позволило в 3–5 раз повысить пропускную способность испытательных станций.
Улучшению производства фарфоровых изоляторов способствовала специализация заводов, проведенная в 1933 г. Заводы «Пролетарий» и «Изолятор» стали специализироваться на выпуске аппаратных изоляторов, завод «1 Мая» — на изоляторах для линий связи и электроустановочных изделиях, а завод им. Артема — на выпуске линейных (подвесных и штыревых) и станционных (опорных и опорно-штыревых) изоляторов. На рис. 10.4 показаны основные типы опорных изоляторов, каждый из них состоит из фарфорового элемента и арматуры. Фарфоровые элементы либо полые (рис. 10.4, а и б), либо сплошные с небольшими выемками для внутренней заделки арматуры (рис. 10.4, в). В первых двух конструкциях опорных изоляторов нижняя часть фарфорового элемента закрепляется в чугунном фланце с помощью цементно-песчаного состава. Сверху фарфорового элемента закрепляется чугунный колпак. Опорные изоляторы на напряжения 6 и 10 кВ имеют по одному верхнему ребру и отличаются друг от друга только высотой.
В 1935–1936 гг. изоляторная лаборатория ВЭИ разрабатывает конструкции линейных противогрязевых изоляторов, которые нашли широкое применение [10.21].
Развитие электрификации СССР предъявило повышенные требования к объему выпуска изоляторов и улучшению их качества, что потребовало пересмотра и усовершенствования основных технологических операций. Важное значение в этом отношении имели разработка и внедрение в электрокерамическое производство в 1939–1940 гг. вакуум-пресса для переработки сырой фарфоровой массы с целью удаления из нее газовых включений и равномерного распределения влаги.
Внедрение вакуум-пресса в изоляторное производство позволило исключить трудоемкий процесс — проточку заготовок керамической массы, которая производилась вручную.
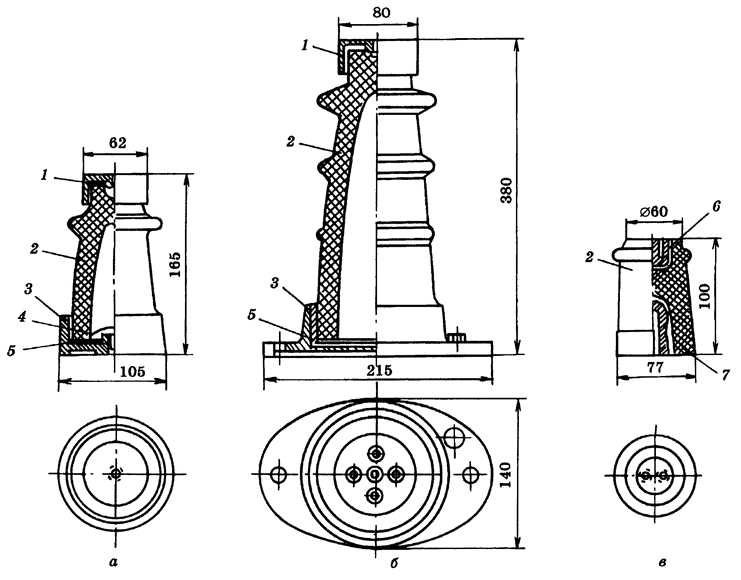
Рис. 10.4. Опорные изоляторы
а — изолятор на 6 кВ с круглым фланцем; б — изолятор на 35 кВ с овальным фланцем; в — малогабаритный изолятор на 6 кВ с внутренней заделкой арматуры; 1 — чугунный колпак; 2 — фарфоровый элемент; 3 — фланец; 4 — колпачок; 5 — картонные прокладки; 6 и 7 — арматура для внутренней заделки в изоляторах
Первыми отечественными изоляторами, изготовляемыми методом протяжки при помощи вакуум-пресса, были модернизированные проходные изоляторы на напряжения 3, 6 и 10 кВ. При этом токоведущий стержень круглого сечения с резьбой на двух концах был заменен плоской шиной, закрепление на цементе двух чугунных колпачков было исключено, что сократило цикл армирования изоляторов. Проходные изоляторы описанной конструкции широко применяются в промышленности начиная с 1940 г.
Для разработки новых электрокерамических материалов и новой технологии и проектирования новых заводов в 1938–1939 гг. в Москве был организован Государственный исследовательский электрокерамический институт (ГИЭКИ).
Этот институт во время войны в 1941 г. был эвакуирован на Урал, где его немногочисленные сотрудники провели ряд важных работ по исследованию и применению уральского сырья в изоляторном производстве, что помогло развернуть работу по производству изоляторов на организованном заводе «Урализолятор» (г. Камышлов).
В 1939–1941 гг. ВЭИ совместно с заводом «Изолятор» разрабатывает маслонаполненный ввод на напряжение 400 кВ для трансформаторов Куйбышевской ГЭС. Эта работа была прервана начавшейся войной.
Дальнейшие интенсификация и совершенствование изоляторного производства развиваются по линии механизации и автоматизации процессов, внедрения высокопроизводительных станков-автоматов и перевода серийного производства на поточный метод.
Бурное развитие изоляторной промышленности происходит в послевоенный период. Осваивается производство линейных изоляторов с гарантированной прочностью 1?105 и 1,57?105 Н. Изоляторная промышленность осваивает выпуск новых типов изоляторов на напряжение 330, 400 и 500 кВ. В 1949 г. начинаются разработки и освоение производства высоковольтных вводов с бумажно-масляной изоляцией, позволившей значительно снизить их массу. В 1959–1960 гг. выпускаются вводы на напряжения 110, 150, 220, 330, 400 и 500 кВ для трансформаторов, установленных на Каховской ГЭС, линиях электропередачи Волгоград — Москва, Волгоград — Урал.
Таким образом, фарфор имеет чрезвычайно широкое применение в электротехнике. Однако он имеет и недостаток — большие диэлектрические потери, сильно возрастающие при повышении температуры, что затрудняет применение фарфора при высоких частотах и температурах.
Развитие радиоэлектронной промышленности вызвало необходимость в новых керамических материалах, обладающих повышенными свойствами. Развитие этих материалов сначала шло по линии усовершенствования фарфора, а затем по линии получения керамических материалов другого состава.
В 1937–1938 гг. Н.П. Богородицкий провел исследования электрокерамических материалов, способных работать в электрических полях высокой частоты, которые имели большое значение для производства радиофарфора и ультрафарфора. Из этих материалов на заводе «Пролетарий» начали изготовляться многие конструкции высокочастотных установочных изделий и радиоизоляторов.
Следует отметить разработку технологии получения отечественного стеатита в 1944–1945 гг. в ГИЭКИ и освоение производства стеатитовых изоляторов, отличающихся от фарфоровых лучшими механическими и диэлектрическими параметрами. Благодаря малым диэлектрическим потерям этот материал нашел широкое применение в высокочастотных установках.
Широкое использование в специальной и бытовой технике высокочастотных устройств приводит к разработке и освоению выпуска высоковольтных конденсаторов для высокочастотных генераторов. В 1945–1946 гг. впервые в СССР разрабатывается и начинается промышленный выпуск малогабаритных керамических конденсаторов типа ТБК и КВИ, которые позволили заменить слюдяные конденсаторы и значительно снизить стоимостные показатели СВЧ-генераторов. Применение керамических конденсаторов типов ТГК-1К, ТГК-1А, ТГК-2,5 и ПТК-2,5, разработанных в 1952 г., также позволило снизить стоимость генераторов примерно в 2 раза и уменьшить их габариты.
В этот же период расширялись и реконструировались действующие изоляторные заводы, строились новые предприятия. Изоляторный завод в г. Камышлове, Южно-Уральский арматурно-изоляторный завод, заводы «Электроконденсатор», «Комиэлектростеатит», Славянский изоляторный завод. В 60-х годах была пущена первая очередь Пермского завода высоковольтных изоляторов, построены завод в г. Великие Луки и завод «Электрофарфор» в г. Бендеры. Мощность отдельных заводов достигала 10–15 тыс. т электрофарфора в год. Заводы, как правило, специализировались на выпуске отдельных видов изоляторов. Производство линейных высоковольтных (подвесных и штыревых) изоляторов было сосредоточено на заводах им. Артема и Южно-Уральском, высоковольтных керамических конденсаторов — на заводе «Электроконденсатор». Завод «Пролетарий» выпускал в основном аппаратные изоляторы и вилитовые разрядники.
Промышленностью в 50–60-е годы был освоен выпуск изоляторов различного назначения из фарфора, стеатита, кордиерита, титановых и других материалов. В производстве стали использовать глиноземистый и тонкодисперсный высококварцевый фарфор. Механическая прочность изоляторов из этих материалов соответствовала мировым стандартам. В короткое время в промышленности освоены более совершенные конструкции проходных, подвесных и опорных изоляторов. Заводы отрасли перешли на производство подвесных изоляторов для подвески тяжелых проводов на линиях электропередачи напряжением 500 кВ, линейных подвесных высоковольтных изоляторов из стекла. В 1964 г. изготовлены вводы постоянного тока на напряжения 200 и 400 кВ для линии электропередачи Волгоград — Донбасс.
В 60–70-х годах разработаны вводы с твердой изоляцией на напряжения 110 и 220 кВ, что позволило уменьшить их габариты и массу; конструкции вводов с твердой изоляцией для трансформаторов на напряжения 330, 500 и 750 кВ; керамические конденсаторы для наружной и внутренней установки с номинальными емкостями от 300 до 4500 пФ на напряжения до 350 кВ; малогабаритные керамические конденсаторы КСК-3–5 емкостью 6000 пФ на напряжение 3 кВ. По своим характеристикам эти конденсаторы превзошли лучшие зарубежные образцы [10.21].
Ленинградский филиал ГИЭКИ разработал новую серию магнитно-вентильных разрядников на напряжения 3–10 и 110–500 кВ с высокими эксплуатационными характеристиками. Здесь же разработана новая серия высокопрочных опорных изоляторов с механической прочностью до 2?104 Н?кг, позволяющая в 2–3 раза снизить массу разъединителей на напряжения 220, 330, 500 и 750 кВ.
В настоящее время продолжают совершенствоваться конструкции фарфоровых изоляторов и повышается их рабочее напряжение. Так, например, заводом «Изолятор» в последнее время разработаны вводы на очень высокие напряжения (500, 750 кВ и выше).
Больше книг — больше знаний!
Заберите 20% скидку на все книги Литрес с нашим промокодом
ПОЛУЧИТЬ СКИДКУДанный текст является ознакомительным фрагментом.