Слесарно-сборочные работы. Виды соединений
Слесарно-сборочные работы. Виды соединений
Все виды соединений деталей, используемые в слесарно-сборочных работах, подразделяются на две основные группы: разъемные и неразъемные. Разъемные соединения – те, которые могут быть разобраны на составляющие детали. В эту группу включены резьбовые, шпоночные, шлицевые, штифтовые и клиновые соединения. Неразъемные, соответственно, те соединения, разборка которых возможна лишь при разрушении крепления или самих деталей. В этой группе прессовые, заклепочные, сварные и клеевые соединения.
Сборка резьбовых соединений
При попытке разобрать какой-либо механизм или слесарное сооружение, будь то двигатель стиральной машины или объект сантехнического оборудования, можно заметить, что большую часть всех соединений деталей составляют именно резьбовые. И это не случайно: резьбовые соединения просты, надежны, взаимозаменяемы, их удобно регулировать.
Процесс сборки любого резьбового соединения включает в себя следующие операции: установка деталей, наживление, завинчивание, затяжка, иногда дотяжка, по необходимости установка стопорных деталей и приспособлений, предохраняющих от самоотвинчивания.
При наживлении ввертываемая деталь должна быть подведена к резьбовому отверстию до совпадения осей и вкручена в резьбу на 2–3 нитки. Каждый, кому приходилось работать с мелкими винтами, знает, как неудобно бывает держать винт в труднодоступных местах, например снизу. Профессионалы в таких случаях применяют магнитные и другие специальные отвертки. Но если их нет, отчаиваться и клясть неподатливый винт крепкими словами не стоит, задачу можно решить с помощью нехитрого приспособления, которое легко изготавливается буквально за несколько секунд. Из тонкой мягкой проволоки нужно сделать небольшой крючок и поддерживать им винт, пока он не войдет в резьбовое отверстие на несколько ниток. Затем нужно просто потянуть за проволоку – петля раскроется и освободит винт для дальнейшего ввинчивания инструментом.
После наживления на деталь устанавливают сборочный инструмент (ключ или отвертку) и сообщают ей вращательные движения (завинчивают). Завинчивание завершают затяжкой, которая создает неподвижность соединения.
Дотяжку производят в том случае, когда деталь крепится несколькими болтами (винтами). Например, при креплении головки блока цилиндров (в двигателе автомобиля), болты ввинчиваются без предварительной затяжки, а после того как они установлены все, производят дотяжку. Это осуществляется в определенном порядке – по так называемому методу спирали (рис. 50).
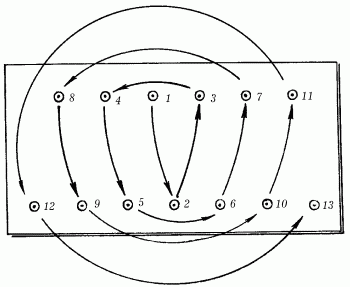
Рис. 50. Схема возможной последовательности затяжки (дотяжки) болтов (винтов, гаек).
Резьбовые соединения в механизмах, подвергающихся в процессе эксплуатации действию пульсирующей нагрузки (вибрации), зачастую сами отвинчиваются, что может явиться причиной аварии. Поэтому при сборке таких механизмов прибегают к стопорению резьбовых соединений.
Самый простой, достаточно надежный и не требующий каких-то специальных приспособлений способ стопорения – это стопорение контргайкой. Ее навинчивают после затяжки основной крепежной гайки и затягивают до полного соприкосновения с ее торцом. Механизм стопорения при таком способе основан на увеличении поверхностей трения в резьбе и на поверхностях гаек.
Широко распространено также стопорение стопорными шайбами (рис. 51).
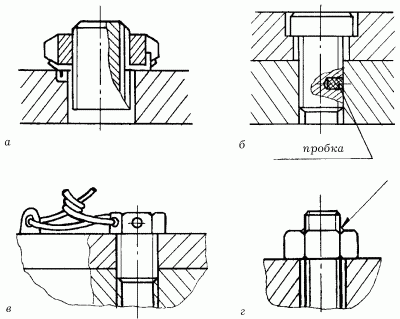
Рис. 51. Способы стопорения резьбовых соединений: а – стопорной шайбой; б – пробкой; в – проволокой; г – сваркой или накерниванием.
Такая шайба имеет либо носик, который отгибают на грань гайки после ее затяжки, либо лапку, которая вставляется в специально просверленное отверстие в корпусе детали. Винты (болты) с открытыми головками можно застопорить проволокой. Отверстия в головках винтов (болтов) под проволоку в этом случае просверливаются до установки их в узел. Проволоку в отверстия следует вводить таким образом, чтобы натяжение ее концов создавало завинчивающий момент.
Стопорение сваркой или накерниванием, по сути, превращает разъемное соединение в неразъемное.
Довольно часто в резьбовых соединениях используют шпильки, которые, в отличие от болта или винта, не имеют головки. Для того чтобы обеспечить плотную посадку шпильки в тело детали, можно воспользоваться одним из предложенных способов: натяг шпильки образуется за счет сбега резьбы (см. главу о нарезании наружной резьбы) либо обеспечивается тугой резьбой с натягом по среднему диаметру витков. Если корпус детали сделан из материала менее прочного, чем шпилька, то используют спиральную вставку из стальной проволоки ромбического сечения: ее вводят в резьбу корпуса детали до ввинчивания шпильки. Этот способ не только повышает прочность и износостойкость соединения (за счет увеличения в корпусной детали поверхности среза резьбы), но и способствует плотной посадке шпильки. Для образования герметичного, гидронепроницаемого соединения между соединяемыми деталями ставят прокладку из легко деформирующегося материала (медно-асбестовую, паронитовую и пр.).
В некоторых случаях требуется получить соединение особой прочности, которой невозможно добиться, применяя обычные болты из низкосортного металла, так как они просто ломаются под большими поперечными нагрузками. Покупать специальные высокопрочные болты дорого, да и не всегда их разыщешь в магазинах. В таких случаях можно перед сборкой нанести на поверхности деталей, которые будут соприкасаться, клеевую прослойку из эпоксидной смолы. Соединение получится весьма прочным даже при использовании обычных дешевых болтов.
Сборка шпоночно-шлицевых соединений
Другим видом неподвижных разъемных соединений являются шпоночно-шлицевые, которые образуются стержнями – шпонками. Шпоночные соединения используются в основном в механизмах для передачи крутящего момента. В зависимости от нагрузки на такие соединения и условий работы механизма используются шпонки клиновые, призматические и сегментные (рис. 52).
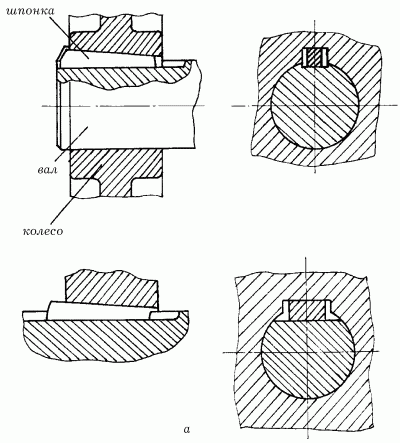
Рис. 52. Разновидности шпоночных соединений: а – клиновой шпонкой.
Рис. 52 (продолжение). Разновидности шпоночных соединений: б – призматической шпонкой; в – сегментной шпонкой; г – шлицевое; д – штифтовое.
Рис. 52 (продолжение). Разновидности шпоночных соединений: е – правильно собранное соединение; ж – дефект увеличенного зазора; з – дефект от перекоса оси шпоночного паза.
Как правило, такое соединение состоит из вала, шпонки и колеса или втулки.
Разновидностью шпоночных соединений является шлицевое, когда шпонка составляет с валом одно целое. Благодаря тому что в этом соединении участвуют не три, а две детали, соединение получается более точным.
При сборке шпоночных соединений вместо шпонки возможно использование штифта. Штифтовое соединение более технологично (что обеспечивается взаимозаменяемостью деталей), но требует дополнительной обработки: в охватывающей детали и на валу необходимо совместно просверлить и развернуть конусной разверткой отверстие под штифт.
Последовательность сборки шпоночного соединения следующая: вал закрепляют в тиски, в паз вала устанавливают шпонку и надевают охватывающую деталь. При этом соединение шпонки с валом должно быть плотным (шпонку устанавливают в паз вала с натягом), в паз же ступицы шпонка устанавливается более свободно.
Когда осуществляется монтаж охватывающей детали (колеса, втулки и пр.) на вал, необходимо проследить, чтобы совпадали оси вала и детали. Неправильное шпоночное соединение приводит к деформации и разрушению шпонки. Основной причиной такого дефекта является увеличенный зазор или перекос оси шпоночного паза. Во избежание дефектов соединений осуществляют пригонку паза шабрением, а также приводят в соответствие размеры пазов и шпонки и контролируют перекосы осей.
Паяные соединения. Лужение
Пайка позволяет соединять в единое изделие элементы из разных металлов и сплавов, обладающих различными физико-механическими свойствами. Например, методом пайки можно соединять малоуглеродистые и высокоуглеродистые стали, чугунные детали со стальными, твердый сплав со сталью и т. д. Особо следует отметить возможность соединения путем пайки деталей из алюминия и его сплавов. Широко применяется метод напайки пластинок твердого сплава к державкам при изготовлении режущего инструмента.
В условиях домашней мастерской пайка – самый доступный вид образования неподвижных неразъемных соединений. При пайке в зазор между нагретыми деталями вводится расплавленный присадочный металл, называемый припоем. Припой, имеющий более низкую температуру плавления, чем соединяемые металлы, смачивая поверхность деталей, соединяет их при охлаждении и затвердевании. В процессе пайки основной металл и припой, взаимно растворяясь друг в друге, обеспечивают высокую прочность соединения, одинаковую (при качественном выполнении пайки) с прочностью целого сечения основной детали.
Процесс пайки отличается от сварки тем, что кромки соединяемых деталей не расплавляются, а только нагреваются до температуры плавления припоя.
Для осуществления паяных соединений необходимы: паяльник электрический или с непрямым подогревом, паяльная лампа, припой, флюс.
Мощность электрического паяльника зависит от размера соединяемых деталей, от материала, из которого они изготовлены. Так, для паяния медных изделий небольших размеров (например, проволоки сечением в несколько квадратных миллиметров) достаточно мощности 50–100 Вт, при пайке электронных приборов мощность электрического паяльника должна быть не более 40 Вт, а напряжение питания – не более 40 В, для пайки крупных деталей необходима мощность в несколько сот ватт.
Паяльная лампа используется для нагрева паяльника с непрямым подогревом и для прогрева паяемых деталей (при большой площади пайки). Вместо паяльной лампы можно использовать газовую горелку – она более производительна и надежна в эксплуатации.
В качестве припоя чаще всего используются оловянно-свинцовые сплавы, имеющие температуру плавления 180–280 °C. Если к таким припоям добавить висмут, галлий, кадмий, то получаются легкоплавкие припои с температурой плавления 70–150 °C. Эти припои актуальны для пайки полупроводниковых приборов. При металлокерамической пайке в качестве припоя используется порошковая смесь, состоящая из тугоплавкой основы (наполнителя) и легкоплавких компонентов, которые обеспечивают смачивание частиц наполнителя и соединяемых поверхностей. В продаже имеются и сплавы в виде брусков или проволоки, которые представляют собой симбиоз припоя и флюса.
Использование в процессе пайки флюсов основано на их способности предотвращать образование на поверхностях деталей окисной пленки при нагреве. Они также снижают поверхностное натяжение припоя. Флюсы должны отвечать следующим требованиям: сохранение стабильного химического состава и активности в интервале температур плавления припоя (то есть флюс под действием этих температур не должен разлагаться на составляющие), отсутствие химического взаимодействия с паяемым металлом и припоем, легкость удаления продуктов взаимодействия флюса и окисной пленки (промывкой или испарением), высокая жидкотекучесть. Для пайки различных металлов характерно использование определенного флюса: при пайке деталей из латуни, серебра, меди и железа в качестве флюса применяется хлористый цинк; свинец и олово требуют стеариновой кислоты; для цинка подходит серная кислота. Но существуют и так называемые универсальные припои: канифоль и паяльная кислота.
Детали, которые предполагается соединить методом пайки, следует должным образом подготовить: очистить от грязи, удалить напильником или наждачной бумагой окисную пленку, образующуюся на металле под воздействием воздуха, протравить кислотой (стальные – соляной, из меди и ее сплавов – серной, сплавы с большим содержанием никеля – азотной), обезжирить тампоном, смоченным в бензине, и только после этого приступать непосредственно к процессу пайки.
Нужно нагреть паяльник. Нагрев проверяется погружением носика паяльника в нашатырь (твердый): если нашатырь шипит и от него идет сизый дым, то нагрев паяльника достаточный; ни в коем случае нельзя перегревать паяльник. Носик его при необходимости следует очистить напильником от окалины, образовавшейся в процессе нагревания, погрузить рабочую часть паяльника во флюс, а затем в припой так, чтобы на носике паяльника остались капельки расплавленного припоя, прогреть паяльником поверхности деталей и облудить их (то есть покрыть тонким слоем расплавленного припоя). После того как детали немного остынут, плотно соединить их между собой; снова прогреть место пайки паяльником и заполнить зазор между кромками деталей расплавленным припоем.
Если необходимо соединить методом пайки большие поверхности, то поступают несколько иначе: после прогревания и облуживания места спайки зазор между поверхностями деталей заполняют кусочками холодного припоя и одновременно прогревают детали и расплавляют припой. В этом случае рекомендуется периодически обрабатывать носик паяльника и место пайки флюсом.
О том, что паяльник перегревать недопустимо, уже говорилось, а почему? Дело в том, что перегретый паяльник плохо удерживает капельки расплавленного припоя, но не это главное. При очень высоких температурах припой может окислиться и соединение получится непрочным. А при пайке полупроводниковых приборов перегрев паяльника может привести к их электрическому пробою, и приборы выйдут из строя (именно поэтому при пайке электронных приборов используют мягкие припои и воздействие разогретого паяльника на место пайки ограничивают 3–5 секундами).
Когда место спайки полностью остынет, его очищают от остатков флюса. Если шов получился выпуклым, то его можно выровнять (например, напильником).
Качество пайки проверяют: внешним осмотром – на предмет обнаружения непропаянных мест, изгибом в месте спая – не допускается образование трещин (проверка на прочность); паяные сосуды проверяют на герметичность заполнением водой – течи не должно быть.
Существуют способы пайки, при которых используется твердый припой – медно-цинковые пластины толщиной 0,5–0,7 мм, или прутки диаметром 1–1,2 мм, или смесь опилок медно-цинкового припоя с бурой в соотношении 1: 2. Паяльник в этом случае не используется.
Первые два способа основаны на применении пластинчатого или пруткового припоя. Подготовка деталей к паянию твердым припоем аналогична подготовке к пайке с использованием мягкого припоя.
Далее на место спайки накладываются кусочки припоя и спаиваемые детали вместе с припоем скручиваются тонкой вязальной стальной или нихромовой проволокой (диаметром 0,5–0,6 мм). Место паяния посыпается бурой и нагревается до ее плавления. Если припой не расплавился, то место паяния посыпается бурой вторично (без удаления первой порции) и нагревается до расплавления припоя, который заполняет зазор между спаиваемыми деталями.
При втором способе место паяния нагревают докрасна (без кусочков припоя), посыпают бурой и подводят к нему пруток припоя (продолжая нагрев): припой при этом плавится и заполняет щель между деталями.
Еще один способ пайки основан на применении в качестве припоя порошкообразной смеси: подготовленные детали нагревают в месте пайки докрасна (без припоя), посыпают смесью буры и опилок припоя и продолжают нагревать до плавления смеси.
После паяния любым из трех предложенных способов спаянные детали охлаждают и очищают место пайки от остатков буры, припоя и вязальной проволоки. Проверку качества паяния производят визуально: для обнаружения непропаянных мест и прочности слегка постукивают спаянными деталями по массивному предмету – при некачественной пайке в шве образуется излом.
Разновидности паяных соединений показаны на рис. 53.
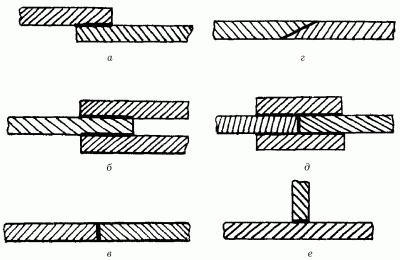
Рис. 53. Конструкции паяных соединений: а – внахлестку; б – с двумя нахлестками; в – встык; г – косым швом; д – встык с двумя нахлестками; е – в тавр.
Лужение
В большинстве случаев детали сначала подвергают лужению, что облегчает последующую пайку. Схема процесса лужения показана на рис. 54.
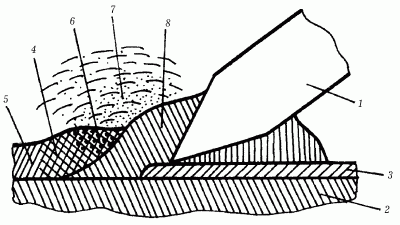
Рис. 54. Схема лужения паяльником: 1 – паяльник; 2 – основной металл; 3 – зона сплавления припоя с основным металлом; 4 – флюс; 5 – поверхностный слой флюса; 6 – растворенный окисел; 7 – пары флюса; 8 – припой.
Однако лужение можно использовать не только как один из этапов паяния, но и как самостоятельную операцию, когда вся поверхность металлического изделия покрывается тонким слоем олова для придания ему декоративных и дополнительных эксплуатационных качеств.
В этом случае покрывающий материал носит название не припоя, а полуды. Чаще всего лудят оловом, но в целях экономии в полуду можно добавить свинец (не более трех частей свинца на пять частей олова). Добавление в полуду 5 % висмута или никеля придает луженым поверхностям красивый блеск. А введение в полуду такого же количества железа делает ее более прочной.
Кухонную утварь (посуду) можно лудить только чисто оловянной полудой, добавление в нее различных металлов опасно для здоровья!
Полуда хорошо и прочно ложится только на идеально чистые и обезжиренные поверхности, поэтому изделие перед лужением необходимо тщательно очистить механическим способом (напильником, шабером, шлифовальной шкуркой до равномерного металлического блеска) либо химическим – подержать изделие в кипящем 10 %-ном растворе каустической соды в течение 1–2 минут, а затем поверхность протравить 25 %-ным раствором соляной кислоты. В конце очистки (независимо от способа) поверхности промывают водой и сушат.
Сам процесс лужения можно осуществлять методом растирания, погружения или гальваническим путем (при таком лужении необходимо использование специального оборудования, поэтому гальваническое лужение на дому, как правило, не осуществляется).
Метод растирания заключается в следующем: подготовленную поверхность покрывают раствором хлористого цинка, посыпают порошком нашатыря и нагревают до температуры плавления олова.
Затем следует приложить оловянный пруток к поверхности изделия, распределить олово по поверхности и растереть чистой паклей до образования равномерного слоя. Необлуженные места пролудить повторно. Работу следует выполнять в брезентовых рукавицах.
При методе лужения погружением олово расплавляют в тигле, подготовленную деталь захватывают щипцами или плоскогубцами, погружают на 1 минуту в раствор хлористого цинка, а затем на 3–5 минут в расплавленное олово. Извлекают деталь из олова и сильным встряхиванием удаляют излишки полуды. После лужения изделие следует охладить и промыть водой.
Сварочные работы
Для создания неподвижных неразъемных соединений широко применяются также сварочные работы, посредством которых между соединяемыми деталями устанавливается межатомная связь.
В зависимости от формы энергии, используемой при образовании сварного соединения все виды сварки делятся на три класса: термический, термомеханический и механический (табл. 1).
Таблица 1. Классификация видов cварки
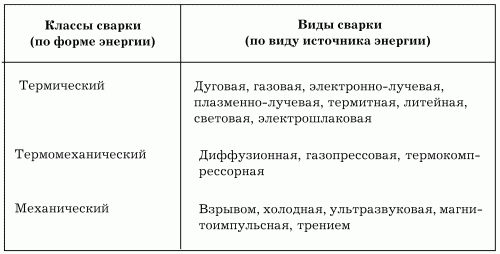
Конечно, далеко не все виды сварки можно осуществить в домашней мастерской. Для большинства из них нужно сложное оборудование. Поэтому более подробно рассмотрим те виды сварки, которые наиболее доступны для домашнего мастера.
Но прежде о подготовке деталей, которые предназначены для соединения сваркой: замасленные места нужно промыть раствором каустической соды, а затем теплой водой, места сварки обработать напильником и органическим растворителем, кромки опилить или отфрезеровать для образования фаски.
Чаще всего в бытовых условиях применяется газовая сварка (рис. 55, а). Принцип газовой сварки заключается в следующем: газ (ацетилен), сгорая в атмосфере, образует пучок пламени, которое расплавляет присадочный материал – проволоку или пруток. Расплавленный пруток заполняет зазор между кромками деталей, в результате чего образуется сварной шов. Газовой сваркой можно сваривать как металлы, так и пластмассу.
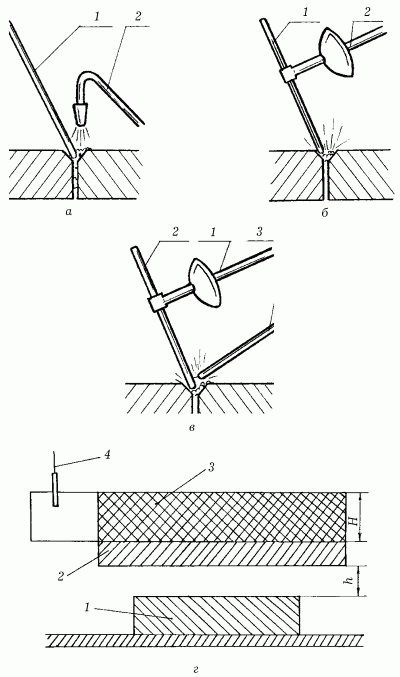
Рис. 55. Виды сварки: а – газовая: 1 – присадочный материал; 2 – сварочная горелка; б – дуговая электросварка плавящимся электродом: 1 – плавящийся электрод; 2 – электрододержатель; в – дуговая электросварка неплавящимся электродом: 1 – электрододержатель; 2 – неплавящийся электрод, 3 – присадочный материал; г – схема сварки взрывом: 1, 2 – свариваемые пластины; 3 – заряд взрывчатого вещества; 4 – электродетонатор.
Так же широко распространена дуговая электросварка (рис. 55 б, в). Ее можно производить как плавящимся электродом, так и неплавящимся – угольным или вольфрамовым (в этом случае в зону плавящей дуги дополнительно вводят присадочный материал).
Средне-, высокоуглеродистые и легированные стали относятся к разряду металлов, обладающих ограниченной свариваемостью. Чтобы избежать трещин при сваривании деталей из этих материалов, их предварительно нагревают до температуры 250–300 °C. Детали из листовой стали толщиной до 3 мм можно сваривать газовой сваркой.
Схема сварки взрывом представлена на рис. 55, г: одну из свариваемых пластин неподвижно устанавливают на основании, над ней на высоте h помещают вторую пластину, на которую укладывают заряд взрывчатого вещества. Электродетонатором взрывают заряд, в результате чего детонационная волна, имеющая высокую скорость и большое давление, сообщает второй пластине скорость соударения. В момент соприкосновения пластин происходит их сваривание.
Остальные виды сварок в домашних условиях провести затруднительно (устройства для диффузионной, лазерной, электронно-лучевой и прочих видов сварки не так широко доступны, как сварочные аппараты для дуговой или газовой).
Сборка заклепочных соединений
Если сборочная единица (узел соединения) в процессе эксплуатации будет подвергаться большим динамическим нагрузкам и способ соединения пайкой не применим вследствие того, что детали изготовлены из металлов, обладающих плохой свариваемостью, то в этих случаях применяют заклепочные соединения.
Заклепка представляет собой металлический стержень круглого сечения, с головкой на конце, которая называется закладной и по форме бывает полукруглой, потайной и полупотайной (рис. 56).
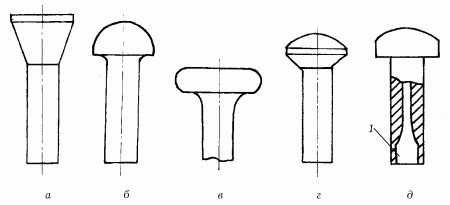
Рис. 56. Виды заклепок: а – с потайной головкой; б – с полукруглой головкой; в – с плоской головкой; г – с полупотайной головкой; д – взрывная заклепка: 1 – углубление, заполненное взрывчатым веществом.
Заклепок сверлят сверлом, имеющим диаметр больше, чем диаметр стержня заклепки. Размеры заклепок зависят от толщины склепываемых деталей.
Саму операцию клепки предваряет подготовка деталей к осуществлению этого вида соединений. Сначала нужно разметить заклепочный шов: если клепка будет происходить внахлестку, то размечается верхняя деталь, для клепки встык размечается накладка.
При этом необходимо соблюдать шаг между заклепками и расстояние от центра заклепки до кромки детали. Так, для однорядкой клепки t = 3d, a = 1,5d, для двухрядной t = 4d, a = 1,5d, где t – шаг между заклепками, a – расстояние от центра заклепки до кромки детали, d – диаметр заклепки.
Далее следует просверлить и прозенковать отверстия под заклепочные стержни. При подборе диаметра сверла следует учесть, что для заклепок диаметром до 6 мм нужно оставить зазор в 0,2 мм, при диаметре заклепки от 6 до 10 мм зазор должен быть 0,25 мм, от 10 до 18 мм – 0,3 мм. При сверлении отверстий необходимо строго соблюдать угол между осью отверстия и плоскостями деталей в 90°.
При прямом методе удары наносятся со стороны замыкающей головки, и для хорошего соприкосновения склепываемых деталей необходимо их плотное обжатие. При обратном методе удары наносятся со стороны закладной головки, и плотное соединение деталей достигается одновременно с образованием замыкающей головки.
Клепку производят в такой последовательности (рис. 57):
– подбирают заклепочные стержни диаметром в зависимости от толщины склепываемых листов:
d = v 2s,
где d – требуемый диаметр, s – толщина склепываемых листов. Длина заклепок должна быть равна суммарной толщине склепываемых деталей плюс припуск для образования замыкающей головки (для потайной – 0,8–1,2 диаметра заклепки, для полукруглой – 1,25–1,5);
– в крайние отверстия клепочного шва вставляют заклепки и опирают закладные головки о плоскую поддержку, если головки должны быть потайные, либо о сферическую, если головки должны быть полукруглые;
– осаживают детали в месте клепки до плотного их прилегания;
– осаживают стержень одной из крайних заклепок бойком молотка и расплющивают носиком молотка;
– далее, если головка должна быть плоской, то бойком молотка выравнивают ее, если полукруглой, то боковыми ударами молотка придают ей полукруглую форму и с помощью сферической обжимки добиваются окончательной формы замыкающей головки;
– аналогичным образом расклепывают вторую крайнюю заклепку, а затем все остальные.
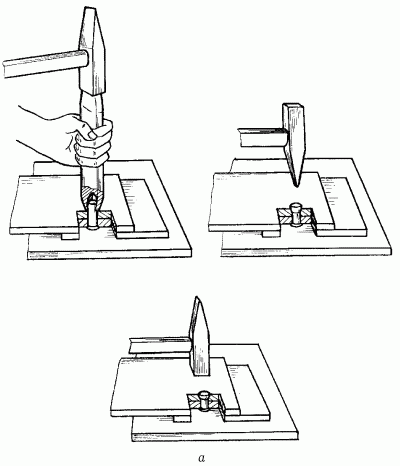
Рис. 57. Последовательность процесса ручной ковки: а – заклепками с потайными головками.
Рис. 57 (продолжение). Последовательность процесса ручной клепки: б – заклепками с полукруглыми головками.
Соединение деталей (преимущественно тонких) в труднодоступных местах производят взрывными заклепками со взрывчатым веществом в углублении (рис. 56, д). Для образования соединения заклепка ставится на место в холодном состоянии, а затем закладная головка подогревается специальным электрическим подогревателем в течение 1–3 секунд до 130 °C, что приводит к взрыву заполняющего заклепку взрывчатого вещества. При этом замыкающая головка получает бочкообразную форму, а ее расширенная часть плотно стягивает склепываемые листы. Этот способ отличается высокой производительностью и хорошим качеством клепки.
Вводить взрывные заклепки в отверстия необходимо плавным нажатием, без ударов. Запрещается снимать лак, разряжать заклепки, подносить их к огню или горячим деталям.
При ручной клепке часто пользуются слесарным молотком с квадратным бойком. Масса молотка для обеспечения качественного соединения должна соответствовать диаметру заклепок. Например, при диаметре заклепок 3–4 мм масса молотка должна быть 200–400 г, а при диаметре 10 мм – 1 кг.
При неправильном подборе диаметра сверла для изготовления отверстия под заклепки, диаметра и длины самой заклепки, при нарушении других условий операции заклепочные соединения могут иметь погрешности (табл. 2).
Таблица2. Брак в заклепочных соединениях и его причины
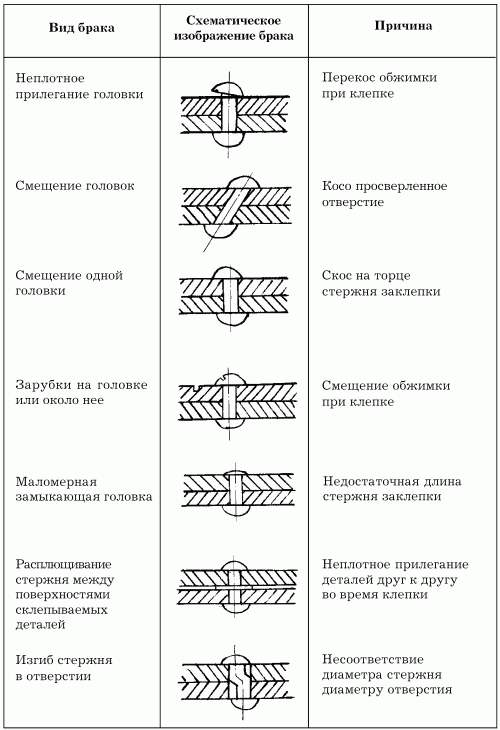
При обнаружении брака в заклепочных соединениях неправильно поставленные заклепки срубают или высверливают и производят клепку повторно.
Значительно облегчают клепку пневматические клепальные молотки с золотниковым воздухораспределителем. При небольшом расходе сжатого воздуха они отличаются высокой производительностью.
Склеивание
Склеивание деталей – это последний вид сборки неподвижных неразъемных соединений, при котором между поверхностями деталей сборочного узла вводится слой специального вещества, способного неподвижно скреплять их, – клея.
У данного вида соединений имеется ряд преимуществ: во-первых, возможность получения сборочных узлов из разнородных металлов и неметаллических материалов; во-вторых, процесс склейки не требует повышенных температур (как, например, сварка или пайка), следовательно, исключается деформация деталей; в-третьих, устраняется внутреннее напряжение материалов.
В слесарно-сборочных работах обычно используются клеи: ЭДП, БФ-2, 88Н (табл. 3).
Таблица 3. Марка клея и область его применения
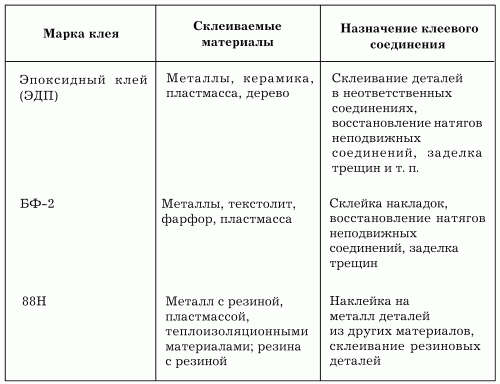
Подобно всем другим видам соединений, качество клееных во многом зависит от правильности подготовки поверхностей к процессу склеивания: на них не должно быть пятен грязи, ржавчины, следов жира или масла. Очистку поверхностей осуществляют металлическими щетками, шлифовальными шкурками, материал для удаления жировых и масляных пятен зависит от марки используемого клея: при склеивании деталей клеем 88Н применяется бензин, под клеи ЭДП и БФ-2 – ацетон.
Процесс склеивания деталей состоит из следующих операций:
– подготовить поверхности деталей и выбрать марку клея (см. выше);
– нанести на поверхности в местах соединения первый слой клея (эту операцию можно выполнять кисточкой либо поливом), просушить, нанести второй слой клея, соединить детали и прижать их друг к другу струбцинами (здесь важно следить за точным совпадением деталей и их плотным прилеганием);
– выдержать клееный узел и очистить швы от подтеков клея.
Режим сушки первого слоя клея: ЭДП наносится в один слой и сушки не требует; БФ-2 требует сушки 1 час при температуре 20 °C («до отлипа»); 88Н – 10–15 минут на воздухе. После нанесения второго слоя выдержать 3–4 минуты и только потом соединить детали.
Режим выдержки клееных соединений: при использовании клея ЭДП – 2–3 суток при температуре 20 °C или 1 сутки при температуре 40 °C; клей БФ-2 – 3–4 суток при температуре 16–20 °C или 1 час при температуре 140–160 °C; клей 88Н – 24–48 часов при температуре 16–20 °C под грузом.
При сборках машин и механизмов иногда используют комбинированные клееные соединения – клеесварные: на сопрягаемую поверхность одной из деталей наносят слой клея ВК-9, а вторую деталь приваривают методом точечной сварки по этому слою.
Больше книг — больше знаний!
Заберите 20% скидку на все книги Литрес с нашим промокодом
ПОЛУЧИТЬ СКИДКУДанный текст является ознакомительным фрагментом.