7.1.2. ЭЛЕКТРОДУГОВОЙ НАГРЕВ
7.1.2. ЭЛЕКТРОДУГОВОЙ НАГРЕВ
Начальный период. В 1878–1880 гг. В. Сименс (Англия) выполнил ряд работ, которые легли в основу создания дуговых печей прямого и косвенного нагрева, в том числе однофазной дуговой печи емкостью 10 кг. Им было предложено использовать магнитное поле для отклонения дуги и регулирования режима перемещения электродов. А. Муассан (Франция, 1890 г.) изготовил дуговую печь для получения карбида кальция.
В конце XIX в. (1899 г.) были созданы первые промышленные дуговые печи. П.Л.Т. Эру построил промышленную печь прямого нагрева для плавки стали (рис. 7.3), а Э. Стассано (Италия) — шахтную электрическую домну для выплавки чугуна из руд, представляющую собой печь косвенного нагрева с вращением наклонной ванны (рис. 7.4).
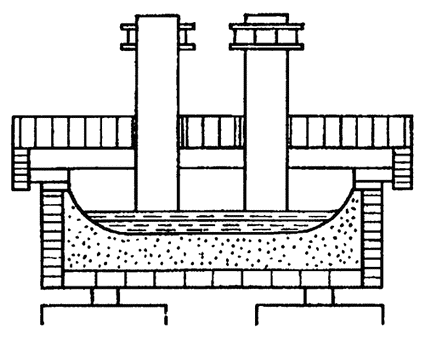
Рис. 7.3. Дуговая электропечь для плавки стали П.Л.Т. Эру
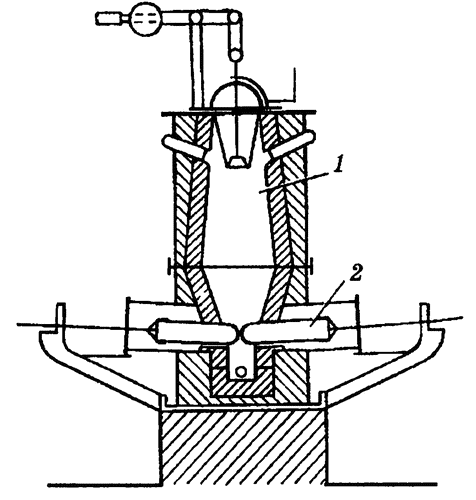
Рис. 7.4. Дуговая электропечь для плавки чугуна из руд конструкции Э. Стассано
1 — шахта; 2 — электроды
Дуговые сталеплавильные печи прямого нагрева. В 1900–1915 гг. были выполнены различные усовершенствования печей конструкции П.Л.Т. Эру и Э. Стассано: печь с тремя электродами, трехфазное питание, подовый электрод, съемный свод, неподвижная ванна, графитизированные электроды, свинчиваемые (наращиваемые) электроды и т.д., которые способствовали распространению дуговых сталеплавильных печей (ДСП) в металлургии.
Использование дуговых печей в России началось с 1910 г., когда на Обуховском заводе в г. Петербурге была установлена двухэлектродная сталеплавильная печь Эру мощностью 500 кВ?А для дуплекс-процесса (мартен — электропечь). Емкость печи 3,5 т при жидкой завалке и 2,5 т при твердой завалке, удельный расход электроэнергии (соответственно) 280 и 865 кВт?ч/т.
Важными этапами для электрометаллургии России и СССР явились:
1910 г. — пуск завода «Пороги» на р. Сатке с печами для получения ферросилиция и углеродистого феррохрома (две печи мощностью по 350 кВт) и производство карбида кальция в печи 250–300 кВт на заводе г. Алаверди.
1916 г. — разработка (С.И. Тельный и В.Г. Евреинов) печи для плавки стали с вращающейся дугой (рис. 7.5).
1917 г. — начало строительства электросталеплавильного завода «Электросталь» под г. Ногинском с установкой четырех печей П.Л.Т. Эру емкостью 1,5 т.
1925 г. — выпуск двух печей с вращающейся дугой емкостью по 0,25 т и мощностью 200 кВ?А для фасонного литья на заводе «Электросила» (позднее Харьковском электромашиностроительном заводе — Л.И. Аронов и А.П. Ионов).
1928 г. — на Московском электрозаводе сконструирована и изготовлена дуговая печь «ГЭТ» косвенного действия для плавки меди (четыре типоразмера печи мощностью 100–325 кВ?А и емкостью 100–1200 кг).
1931 г. — изготовление и пуск в эксплуатацию трехтонных ДСП; 1932 г. — изготовление десятитонной ДСП и первых ферросплавных печей мощностью 800 и 1600 кВ?А.
1928–1934 гг. — на Московском электрозаводе изготовлена 151 дуговая печь емкостью до 12 т (Л.И. Аронов, К.М. Филиппов и др.)
1940 г. — на заводе «Уралэлектромашина» изготовлена ДСП емкостью 30 т (пущена в г. Запорожье).
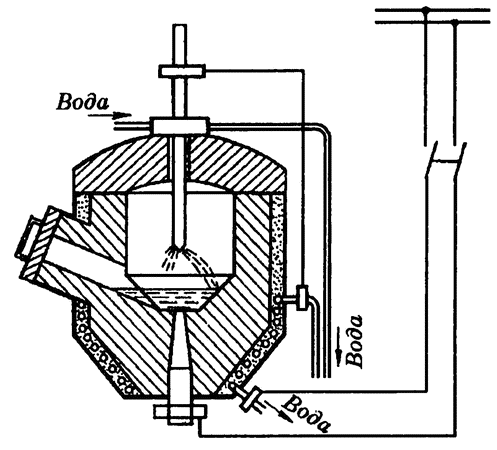
Рис. 7.5. Однофазная печь с вращающейся дугой конструкции С.И. Тельного и В.Г. Евреинова
За годы войны дуговые печи на предприятиях устарели, и появилась необходимость создания новых печей.
В 1949–1952 гг. ОКБ треста «Электропечь» разработало серию дуговых сталеплавильных печей с выкатывающейся ванной типа ДСВ емкостью 5, 10, 18 и 30 т. Всего на МосЗЭТО было изготовлено 40 печей общей емкостью свыше 700 т. В 1951–1953 гг. на заводе «Днепроспецсталь» были пущены в эксплуатацию две печи емкостью по 18 и одна печь емкостью 30 т.
В 1955 г. была разработана печь с поворотным сводом емкостью 80 т. Две такие печи были изготовлены в 1958 г. Новосибирским ЗЭТО и установлены на Новолипецком металлургическом комбинате.
В 1971 г. на волгоградском металлургическом заводе «Красный Октябрь» были введены в эксплуатацию две печи ДСП-200, разработанные ВНИИЭТО. Емкость такой печи 200 т, мощность печного трансформатора (разработан и изготовлен на Московском электрозаводе) 45 MB?А.
Для увеличения производительности ДСП стали использовать трансформаторы более высокой мощности, в частности для печи емкостью 200 т — 90 и 125 MB?А.
Шведская фирма ASEA в 1947 г. разработала для крупных ДСП устройство электромагнитного перемешивания расплавленного металла. В 60-х годах в США стали применять печи емкостью 400–800 т с трансформаторами мощностью до 200 MB?А. В конце 70-х годов фирма «Маннесман» (ФРГ) стала применять систему донной разливки стали и охлаждаемые стены и свод. Все эти разработки были направлены на увеличение производительности печей.
В 80-е годы наиболее перспективными направлениями развития ДСП в нашей стране и за рубежом явились дуговые печи с питанием на постоянном токе, что существенно снизило потери в короткой сети, и печи с водоохлаждаемой футеровкой и сводом для работы в дуплекс-процессе, т. е. практически только для расплавления шихты. Во ВНИИЭТО (А.Н. Попов, Л.С. Кацевич и др.) был проведен ряд исследований и конструкторских разработок в этих направлениях.
Разработанная во ВНИИЭТО ДСП постоянного тока емкостью 12 т была введена в эксплуатацию в 1981 г. В 1984 г. на Оскольском электрометаллургическом комбинате установлены две ДСП емкостью по 150 т с трансформатором 90 MB?А. В футеровке стен печи использованы водоохлаждаемые панели.
Дуговые печи косвенного нагрева. Дуговая барабанная качающаяся печь с двумя горизонтальными электродами разработана в Корневильском университете в 1915 г. (Х.В. Жиллетт) и изготовлена в 1917 г. В 1918 г. фирма по производству электропечей в г. Детройте (США) начала серийное производство этих однофазных печей для переплава медных сплавов. Попытки изменить конструкцию (ввести вращение ванны или три электрода с трехфазным питанием) оказались неудачными. В СССР печи такого типа изготавливались на Московском электрозаводе с 1929 г. В настоящее время дуговые печи косвенного нагрева не выдерживают конкуренции со стороны индукционных плавильных печей.
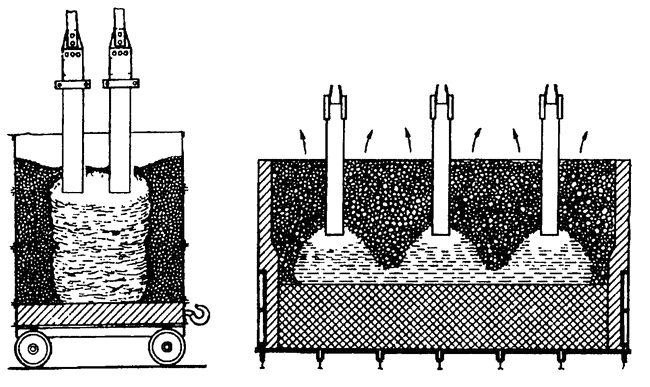
Рис. 7.6. Открытая трехфазная печь для получения карбида кальция конструкции А. Хельфенштейна
Рудовосстановительные (руднотермические) печи. В начале XX в. были созданы двухэлектродные печи постоянного или переменного тока для производства карбида кальция мощностью до 4000 кВ?А. Эти печи использовались также для производства ферросплавов. А. Хельфенштейн (Австрия) ввел в эксплуатацию трехфазные печи мощностью до 12 MB?А (рис. 7.6) с проводящим угольным подом, присоединенным к нейтральному проводу. В 1907 г. в Норвегии была пущена печь мощностью 24 MB?А, представляющая собой практически сдвоенную печь (две трехфазные системы в одном кожухе). Для улучшения условий труда уже в 1910 г. была создана конструкция полузакрытой печи с отсосом газов.
С 1895 г. разрабатываются конструкции электропечей для получения чугуна из железной руды. В 1908 г. в Швеции была построена дуговая печь (электрическая домна) мощностью 700 кВт с питанием от сети 25 Гц. В дальнейшем в Швеции и Норвегии были пущены несколько подобных усовершенствованных печей: двухфазная с четырьмя электродами мощностью 1850 кВт с использованием древесного угля, трехфазная с шестью электродами, а в 1913 г. трехфазная конструкции А. Хельфенштейна мощностью 7360 кВт с использованием кокса. В 1925 г. в Норвегии (фирма «Электрохемикс») была введена в эксплуатацию первая закрытая низкошахтная прямоугольная печь мощностью 6 MB?А.
В СССР первые ферросплавные печи (открытые) мощностью 800 и 1600 кВ?А изготовлены Московским электрозаводом в 1932 г. В 1934 г. в г. Запорожье пущены печи фирмы «Мигэ» (Франция) мощностью 10 MB?А для получения алюмината бария и ферросилиция. Закрытые печи стали создаваться с середины 30-х годов.
По разработкам ВНИИЭТО в СССР построены и пущены различные руднотермические печи.
В 1958 г. пущена первая закрытая ферросплавная печь мощностью 10,5 MB?А на Кузнецком ферросплавном заводе. В 1978 г. созданы и внедрены на Никопольском ферросплавном заводе печи мощностью 63 MB?А для получения марганца и силикомарганца. В 80-е годы созданы и внедрены руднотермические печи мощностью 80 MB?А для возгонки желтого фосфора, 63 MB?А для получения ферросилиция и марганцевых сплавов, 40 MB?А для производства силикохрома. Печи для возгонки желтого фосфора, выпускавшиеся в СССР в 70–80-е годы, питались от трех однофазных трансформаторов с подключением к сети 110 кВ и по ряду показателей превосходили фосфорные печи США и ФРГ.
В начале 80-х годов фирма «Элкем» (Норвегия) ввела в эксплуатацию закрытую печь для производства феррохрома мощностью 105 MB?А.
Вакуумные дуговые печи. Вакуумно-дуговая плавка предложена в 1905 г. В. фон Больманом (Германия). В. Кролл (США) в 1940 г. осуществил вакуумно-дуговую плавку титана. Имеются два варианта вакуумно-дуговых печей (ВДП): с расходуемым (переплавляемым) и нерасходуемым (водоохлаждаемым) электродом. Второй вариант применяется реже, например для плавки слитков из губки или порошка (патент Англии, 1957 г.). Количество ВДП быстро увеличивалось, например, &США за три года (1957–1959) оно почти удвоилось. При этом жаропрочные и шарикоподшипниковые стали плавили в ВДП, получая слитки диаметром до 600 мм и массой до 6 т. Промышленные ВДП для титана созданы в 1948–1950 гг. Вакуумная плавка тугоплавких металлов (молибден, ниобий, вольфрам) позволила получать слитки массой до 1 т (конец 50-х годов).
В СССР работы по ВДП начались с середины 50-х годов в ряде организаций: Институт металлургии им. А.А. Байкова АН СССР (Имет), ЦНИИ черных металлов (ЦНИИчермет), МЭИ. Изготавливались и разрабатывались первые ВДП на Московском заводе электровакуумных печей (М.Я. Смелянский). В 1970 г. осуществлен пуск ВДП, разработанной во ВНИИЭТО, для производства слитков массой 60 т в г. Ижоры. В 80-е годы ВНИИЭТО разработал новую серию вакуумно-дуговых печей для плавки стали и тугоплавких металлов, в которых использовались электроды большего диаметра, кристаллизаторы различной формы сечения, подача инертного газа и другие конструктивные новшества.
Установки электрошлакового переплава. Первые в мире электрошлаковые печи (ЭШП) были разработаны и изготовлены Институтом электросварки АН УССР им. Е.О. Патона (ИЭС) и в 1958 г. введены в эксплуатацию на заводе «Днепроспецсталь» и Новокраматорском машиностроительном заводе. В ряде стран (Франция, Япония, Швеция и др.) установки ЭШП сделаны и эксплуатируются по лицензиям СССР.
В 60–70-е годы ВНИИЭТО совместно с ИЭС создал ряд промышленных установок ЭШП: для производства слитков массой 10 т в г. Краматорске (1962 г.), 60 т в г. Ижоры (1968 г.), для получения полых и прямоугольных слитков массой 16 т (1975 г.), круглых слитков массой 200 т и диаметром до 2, 4 м, предназначенных для изготовления роторов турбин (1978 г.). В 1977 г. была создана печь для электрошлакового литья емкостью 5 т.
В 80-е годы получили распространение ЭШП для кокильного и центробежного литья, разработанные ИЭС.
Больше книг — больше знаний!
Заберите 20% скидку на все книги Литрес с нашим промокодом
ПОЛУЧИТЬ СКИДКУДанный текст является ознакомительным фрагментом.